The closer the engine project gets to being done the harder it is to keep working on it. If I’m honest with myself I know it is because I doubt my abilities and I don’t want to be found out. This self destructive anxiety shows its ugly head every once in a while and I have to recognize it to get past it. The only way I can get past it is to recognize when i have been inside my head for 30 minutes while thinking about all the things that could be wrong with the job rather than actually doing the job. Once I recognize it I have to immediately pick up a toll or a part and start physically doing the job. It is my only cure for the analysis paralysis that affects me.
I did get down to the shop yesterday and noticed that I had been down there for the first half hour without actually making any progress on the engine. I immediately grabbed the intake manifold and got to work. Unfortunately I was so flustered by this mental weakness that I wasn’t paying close enough attention to a very important detail. As I was torquing down the lower intake manifold I noticed that the first step was 44 then 88 then 11, this made no sense but I started anyway. I hadn’t even got it to 44 when it felt wrong. The gasket is a hard plastic with a silicone seal embedded in it. As I got the first bolt down to 44 i heard a crack. I immediately stopped and went back to the computer.
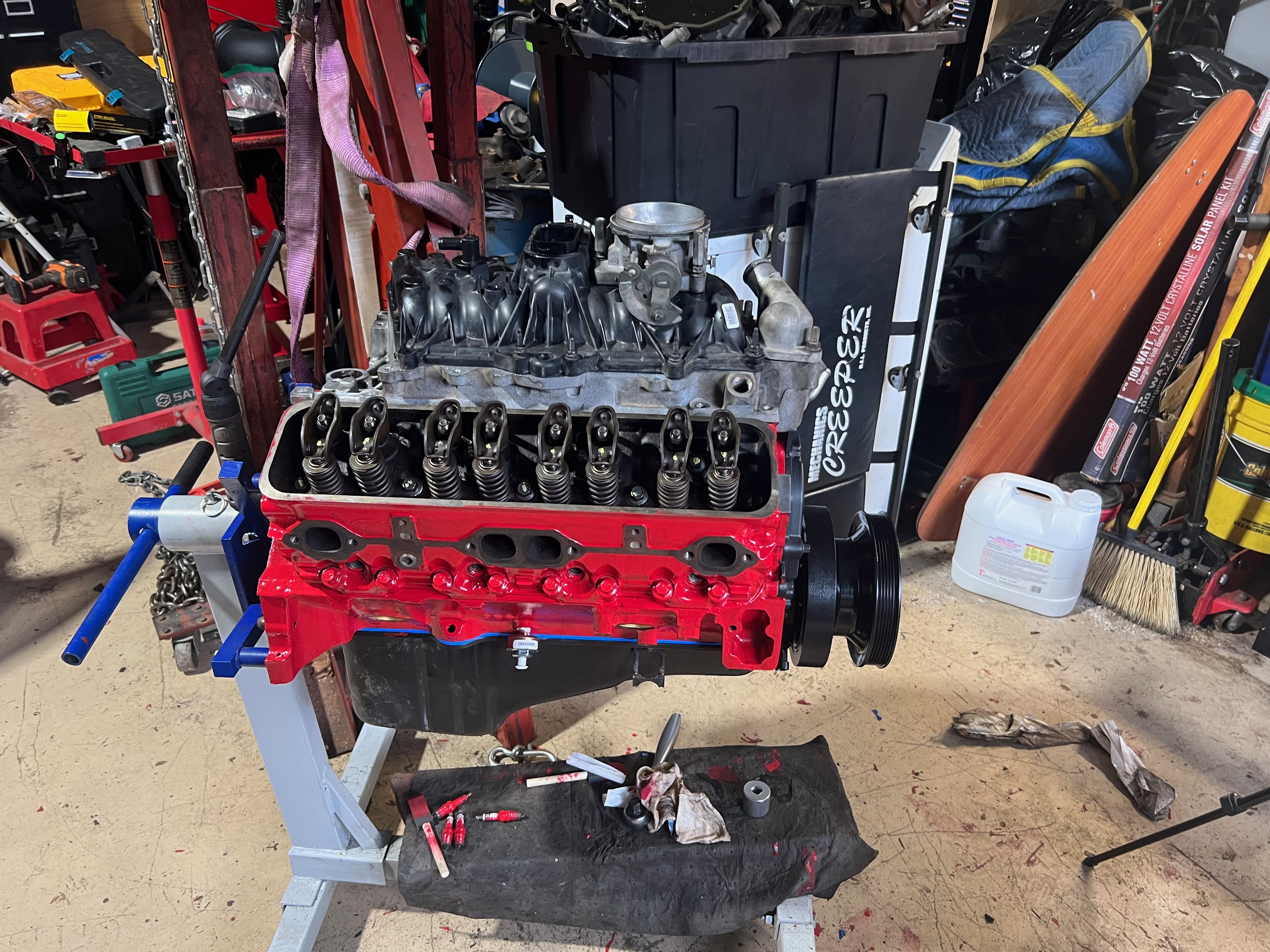
I have been looking for a decent source of correct information about this engine. I have no idea why but although I have a manual for the truck on 2 CDs, it is painful to find anything. I am almost tempted to print the damn thing out. I broke down and bought the Haynes manual which will be sent to me this week and in the mean time I looked at the online version to find the correct specs. To my horror I had the correct specs, the Hanes manual on the other hand had slightly more information. The specs are 44 INCH POUNDS! then 88 INCHE POUNDS, then 11 FOOT POUNDS.
I immediately backed off the bolts I had been crushing the gaskets with and removed the intake manifold. I checked the gasket for any damage and found none. I put a much better bead of RTV on each end between the gaskets and ran all the bolts through the wire brush. I reviewed a Youtube video of a guy that had done a beautiful job of rebuilding his engine and noted that he used blue thread locker for the bolts and did the same. I found my 1/4 torque wrench and complained bitterly about how small and faint the markings for the inch pound gage were. I then set it correctly and followed the torque pattern and got all the bolts snugged down to 1/12th of what then were before. I then went up to 88 inch pounds and knowing that my 3/8 torque wrench only goes down to 20 foot pounds. I did the mental math of 11 foot pounds time 12 to make it 132 inch pounds and snugged all the bolts down correctly in the spiral torque pattern.
I checked both ends and cleaned up some of the squeeze out of the RTV which assured me it is sealed. I am happy with that job . I am not as happy with the cleanup job I was able to manage on the intake manifold as a whole and the rebuild of the injectors was a PITA due to how tight they are when pushing against new O rings getting them back into the spider body. But I need to keep moving forwards and just note that if something is not right when it starts, there will be a list of things to re-visit. This is going to be the only way to finish this project, the other option being to buy more new parts, but at some point it has to go back together and be done.
I started putting more pieces on the intake manifold and then stopped. I think I need to get this back in the truck before I put anything else on it. Well except for the engine mounts and the flex plate. I also need to figure out how to torque the harmonic balancer bolt to 60 foot pounds without the engine turning.
With these things in mind I decided to work on the water pump. It was pretty new, I think I replaced it about a year ago, but I didn’t realize it wasn’t coated with anything. When I removed it I was surprised at just how rusty it had become. I ran it under the wire wheel and got off most of the rust on the large surfaces. I used a wire brush that fits the drill to get to some of the nooks and crannies. During this exercise the brush bounced off the part and hit my arm. It immediately grabbed onto my nylon sleeves that I wear to keep the sun off my forearms. It twisted it up and due to the immense strength of the nylon , it ripped the drill out of my hand. This is the ONLY time that I have been glad that this drill doesn’t have a way to lock it in the ON position. I twisted the drill counter clockwise to unwind the nylon until it finally let go. I counted three full rotations. My sleeve when right back to it’s normal shape with only a few strands having broken in the méle. A coat of bare metal etching primer and then 3 coats or gloss black engine enamel and the water pump will not rust again. Well at least not from the outside.
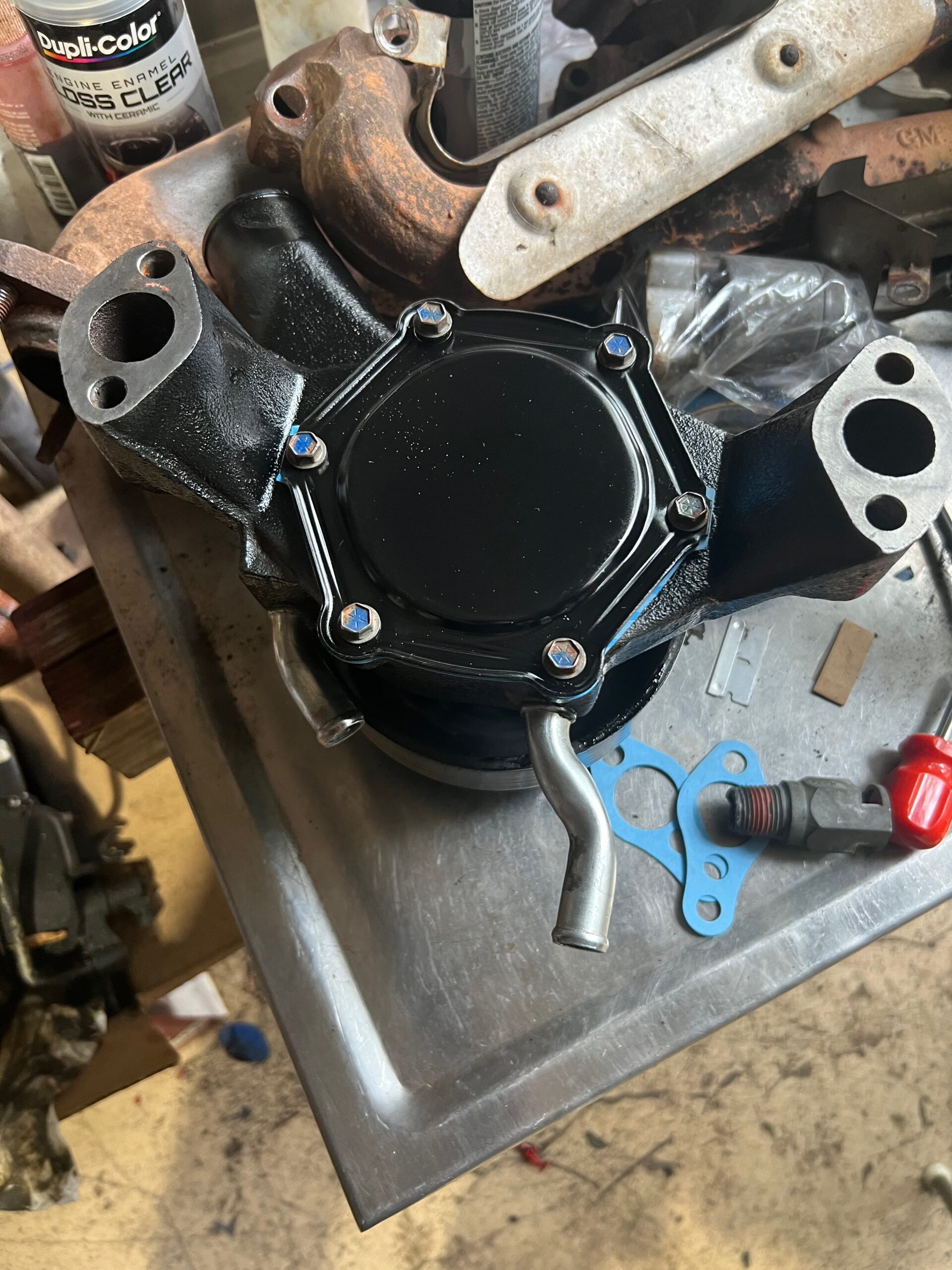
As I was about to leave I decided to throw the valve covers on the block to see what they look like. It is also a good way to keep crap and insects from getting in the engine.
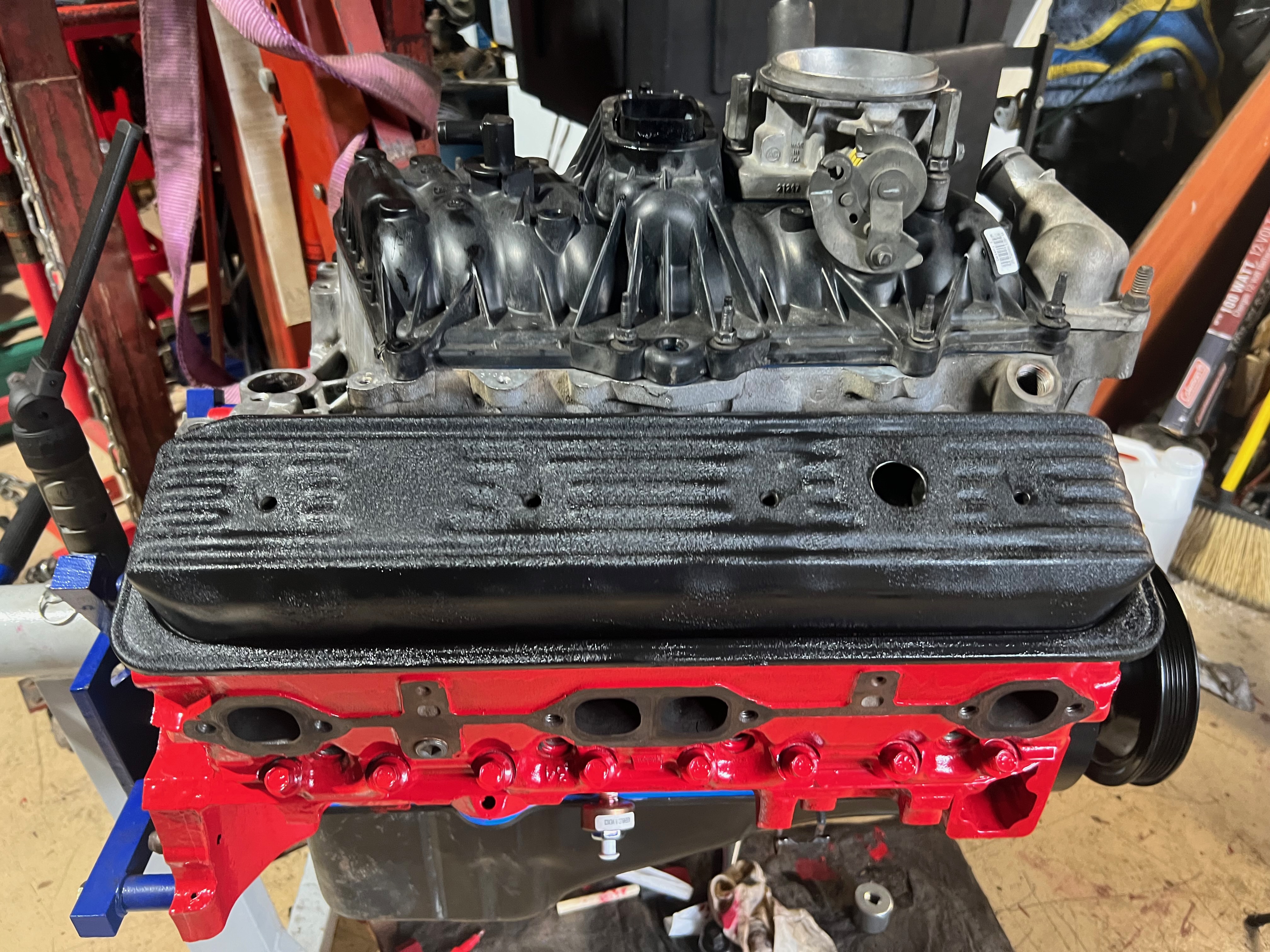
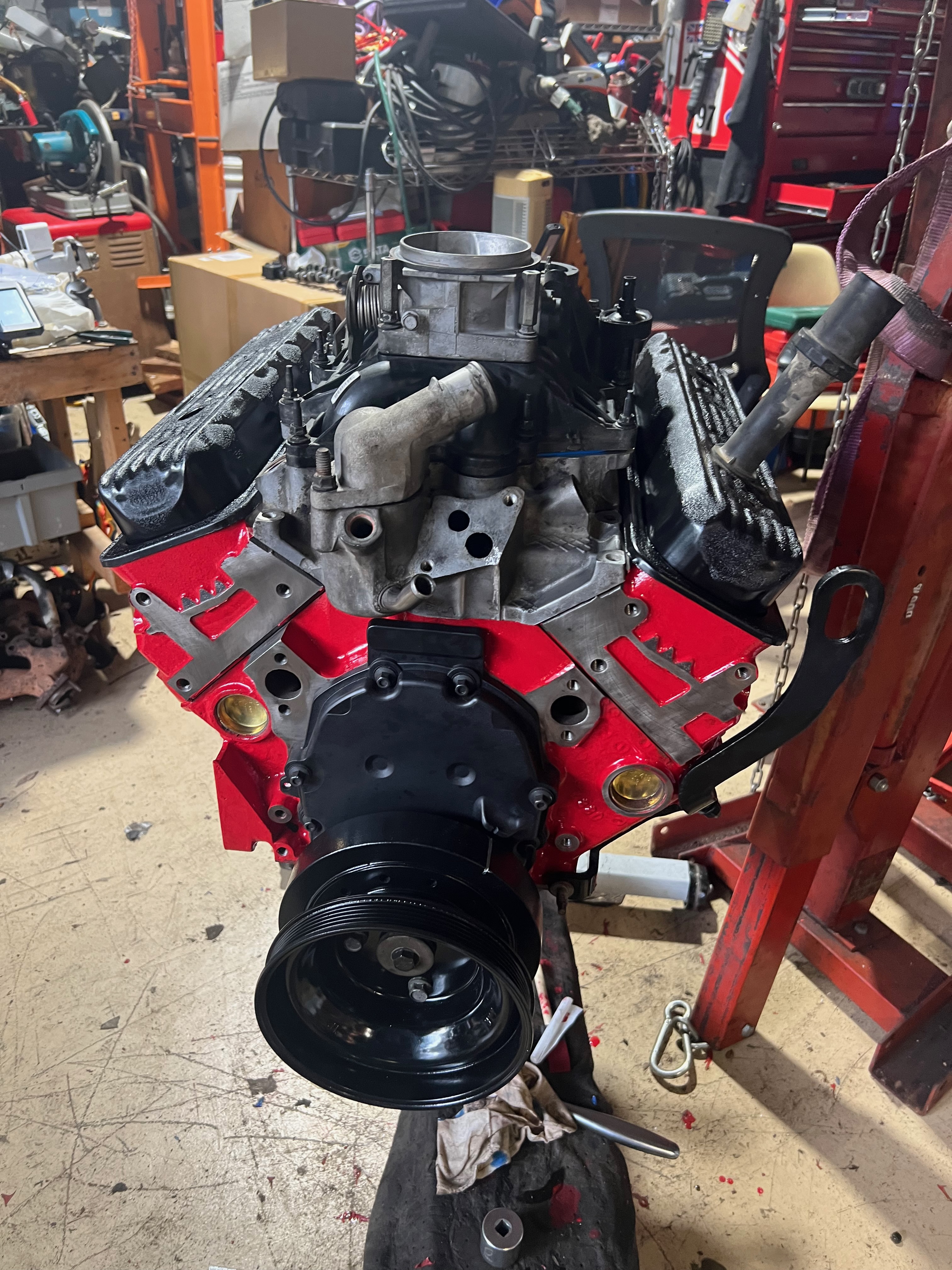
They look very “Finished” much like I wish I was. At least I am closer than I was this morning.