While it is true that I would rather be hot than cold. Some heat is downright dangerous. This morning by the time I got to the shop it was 80 and 70 percent humidity. Just pulling the truck in with the come along made me sweat and have to take off my cap.
I knew it was going to be a long and mostly unproductive day. I sat there staring at the front of the truck felling the fan blow the hot air across my feet and wondering what it was going to take for me to get up and move the fan. I drank some more ice water and looked through the Haynes manual for the torque specs on the flex plate to torque converter bolts. After getting up and adjusting the fan to its highest angle I grabbed the 1/2 inch torque wrench and sat back down to enjoy the hot air blowing full force on my knees. Not a total win but slightly better than before. Seems like that is going to be the theme for the day. With the three bolts the torque wrench and my magnetic based mechanics light, I sat there wondering when I would shame myself into getting started. So I decided to call my parents.
Lately they have announced a few maladies. Some more serious than others. They are in their late seventies and in better shape than me. that is actually not an exaggeration. My sister just spent a week with them, helping them get a couple of things taken care of. All while getting a free place to stay while in town for a reunion. Although I’m sure in her mind it is the other way round. While she was here she scheduled someone to go by their house to get their riding lawnmower running. I had made a valiant effort almost a year ago. When I had dad buy a new carb and we sat together to replace it. It was a good but frustrating day. Other engine would run fine with starter fluid but die without it.
This guy did all the things I would have, and found the issue. This time when the “new” carb was removed it was totally contaminated with water. Turns out dads frugality had sabotaged our previous efforts. The fuel tank was 3/4 full of water. The old gas can he filled it with must have been bad. I’m glad he found the issue, but now he needs another new carb.
Well I can’t really think of anything else to procrastinate from having to crawl on my back under the truck, So I gathered some tools and some parts and slid my fat back under the truck. I have a crawler but that 2″ of clearance makes all the difference in the world for this truck. It is not on jacks or ramps, it is just sitting at its normal height. I can get und all but the lowest parts. The skid plate under the transfer case is low and the rear axle is very low but almost everything else is manageable.
First job is the torque converter, there are three bolts that hold it to the flex plate but you can only see two at a time. one on each side of the oil pan and really the only accessible one is the one by the starter hole. I manage to turn the engine using the big torque wrench and an extension. it is cumbersome and fall off more that it turns but I manage to get one hole accessible. I get the 1/2 in long both threaded and then crank it down. I use the same horrible method to get the second bolt lined up and it won’t go in. I have broken the cardinal rule when assembling something with multiple bolts. Never fully tighten anything until all of the bolts are started. This requires a water break.
One eight oz bottle of lukewarm water later, I have a new plan I take with me a couple of chunky screw drivers and a hammer. Just the sort of tools that hack mechanics use rather than doing things the right way. Well I am hot, tired sore and annoyed so tempering my feelings I bring a dead blow hammer with a copper face rather than the BFH Jr. I had planned on.
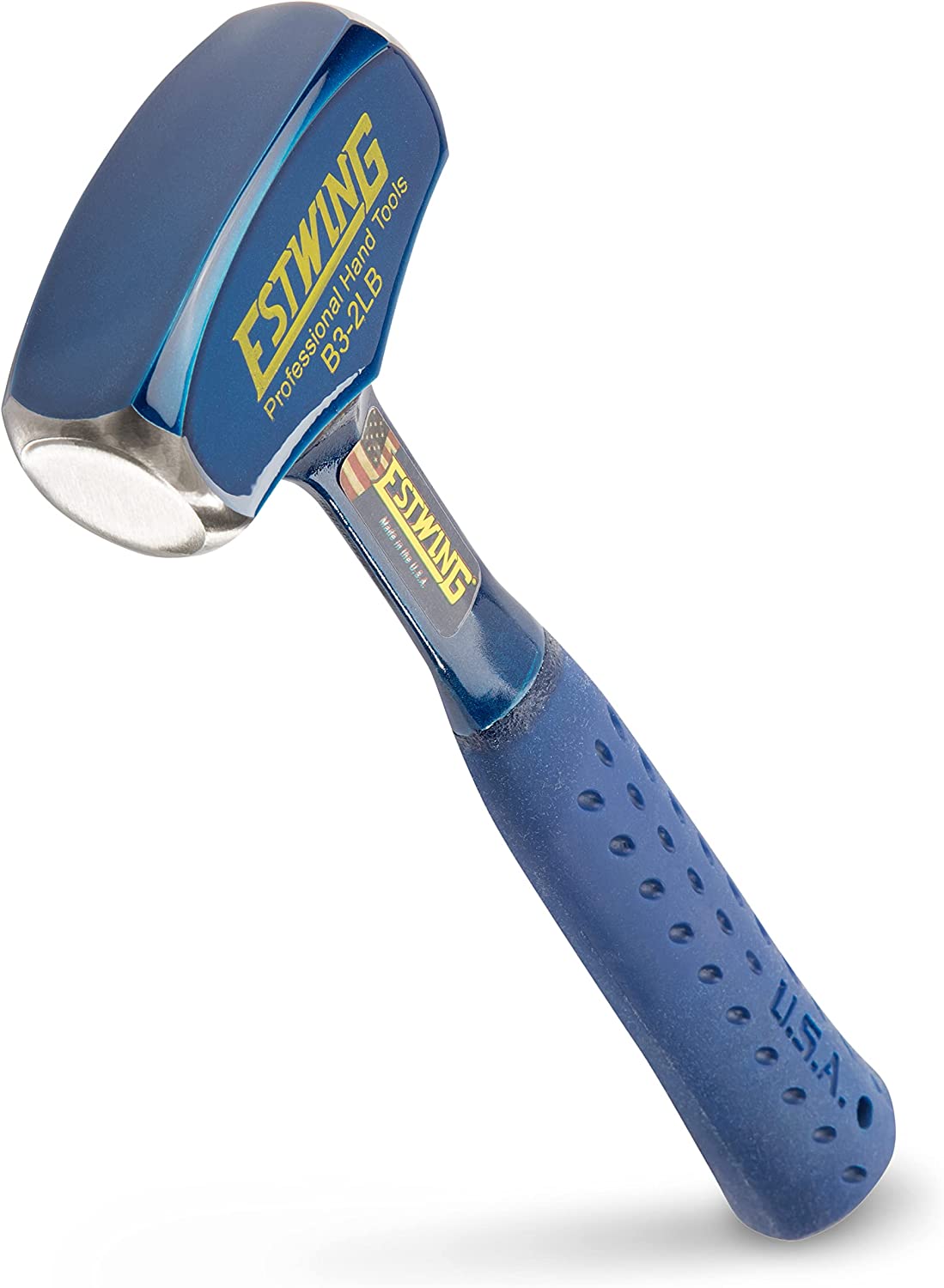
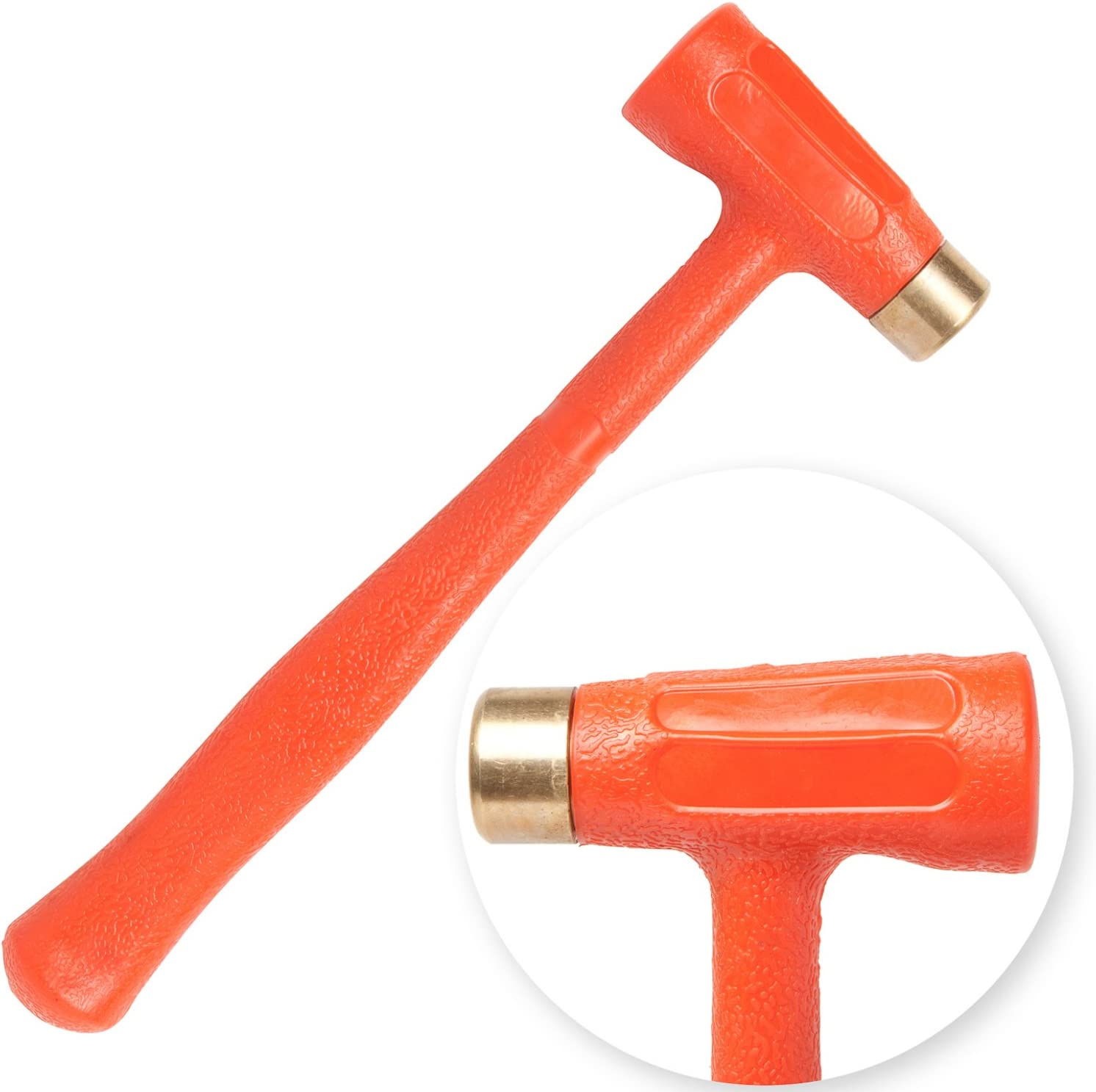
Back under Betty I place the screwdriver on the welded on mounts that hold the captured nut on the torque converter. I know the nut needs to be a little further than the the hole is so I give it a couple of love taps to encourage it to shift it. No luck, even a brisk and unsatisfying bash does nothing because this hammer although only 1/2 a pound lighter is relatively gentle compared to the heft and authority of the two pound steel head and handle of the BFH Jr. that I had originally opted for. The bolt gains traction into the hole but at a less than optimal angle but it straightens itself as it goes in and I tighten it down. One left. Not wanting to drag myself from under the truck again, I decided to try to move the engine by levering the flex plate teeth clockwise via the inspection hole in the bell housing. I get it to move about 1/3 of an inch at a time but it is moving and i don’t have to get out so I keep it up until the third hole is showing. This is the bolt that has to go in the hole that is slightly less than perfect. When removing the engine it was the only one I had not been able to get to. Remember the whole reason I was taking it apart was because it was frozen so I could not turn it to get to this bolt. Anyway. It hung up on the torque converter and bent the flex plate slightly. I had bashed it flat again with the use of said hammer and it was almost perfect. But not quite. This bolt had no chance of going in, and i knew it. I screwed up tightening the first one fudged it by bashing the mount to get the second one to go but this third one was so far off I knew the only solution was to loosen the other two to get this one to line up.
This is one of those tasks that I know is going to take a long time and effort and I know it is my fault so in my head I punish myself as I go through the task. I see the small pieces of metal being shaved off by the screw driver each time a I pry on the flex plate to get tit to turn. I convince myself this is why the starter takes more power than it should to turn the engine and that I have probably destroyed the teeth beyond repair. Luckily this task takes a long time and I have a short attention span so after the internal berating I notice that the metal shavings are actually coming from the edge of the inspection hole on the aluminum bell housing and that the flywheel is not being damaged in the slightest and even if it was I am grabbing the back half of the teeth that the starter probably doesn’t even engage with. Man that internal critic is such an ass. Back in reality I managed to back off the two bolts and get the third hole back in view. This time I can see it is mis aligned but i can also move the flex plate and torque converter independently. With my flathead screwdriver/pry bar/bolt aligner, I managed to get the threads dead center of the hole and the bolt goes in beautifully. It does take a little extra to get the plate to flatten out for that bolt but it does it before I reach the 65 pound torque setting. A few more prys with the screwdriver at a regular pace and the other two bolts get torqued to spec. Holy crap something got achieved. I need some more water.
Mildly refreshed, I find all of the bolts for the bell housing cover in a bag named “Bell housing cover bolts”, which genius did that 😉 So after a quick wipe down with degreaser and a rag i slide back under with a 10mm ratcheting wrench I get all the bolts in snugly and give them a final turn to a tightness that makes me happy that they won’t work out but not so tight I am starting to strip out the aluminum. This is a feel sort of thing that can only be achieved by years of losing bolts that weren’t tight enough and having to find larger bolts to replace ones you just stripped out. And no there is not a correct torque setting for these screw threads.
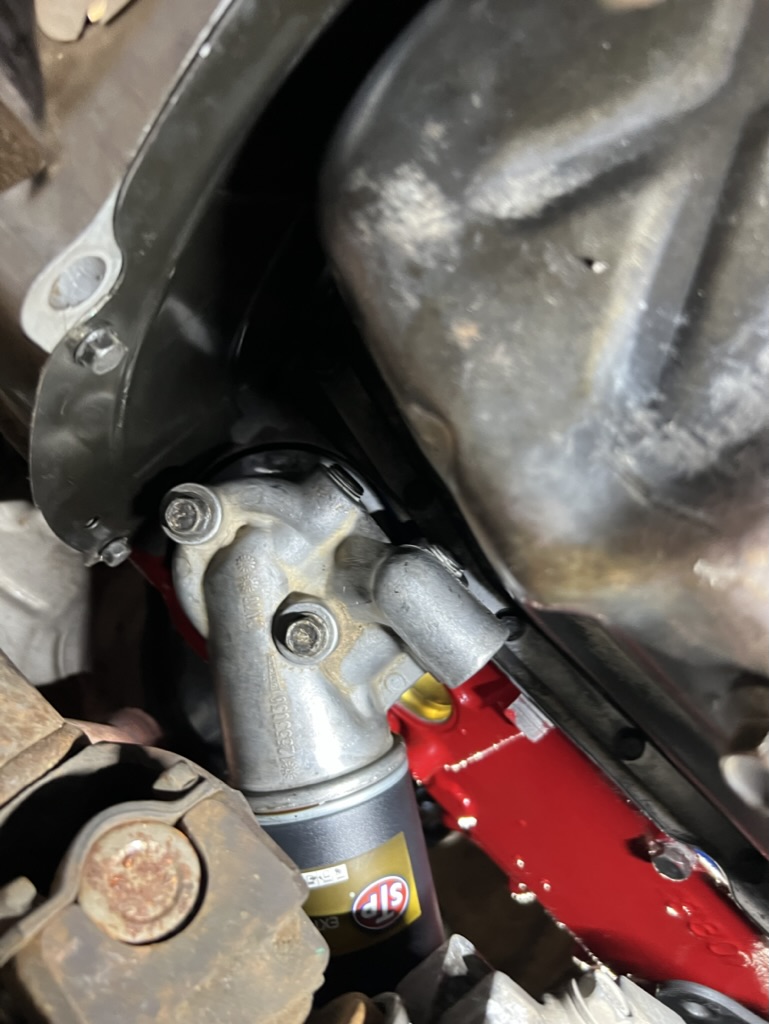
I’m starting to feel pretty good about progress, so I grab the next parts to install down under. There are a couple of rods that go from the bell housing to the engine mounts, they are structural and hold the transmission in place. They are also almost impossible to put in place with the engine and transmission in the truck. for the drivers side you can actually see where the rod goes in the image above. The bolt end goes through the hole in the transmission bell housing at the upper left corner of the image. and the lower flattened bar with a hole in it gets bolted through the flat bar with a hold that hangs from the engine mount that is visible at the very bottom right hand corner of the image. The bell housing bolt is no problem. The upper mount is very difficult to get even one hand on. So one hand holding a rod a bolt and a nut that all need to be aligned together and threaded is damn near impossible. The thought of trying to get two hands in there is physically, absolutely impossible. It took about 20 minutes and every curse word I knew to get it threaded using the two wrenches to tightened it required new words and some jibberish. By the time I had the second side connected my eyes and my mouth had managed to collect any extra chunks of oil that were not cleaned up before the engine when back in and my vocabulary was exhausted. Below is a shot of the drivers side rod connected to the motor mount.
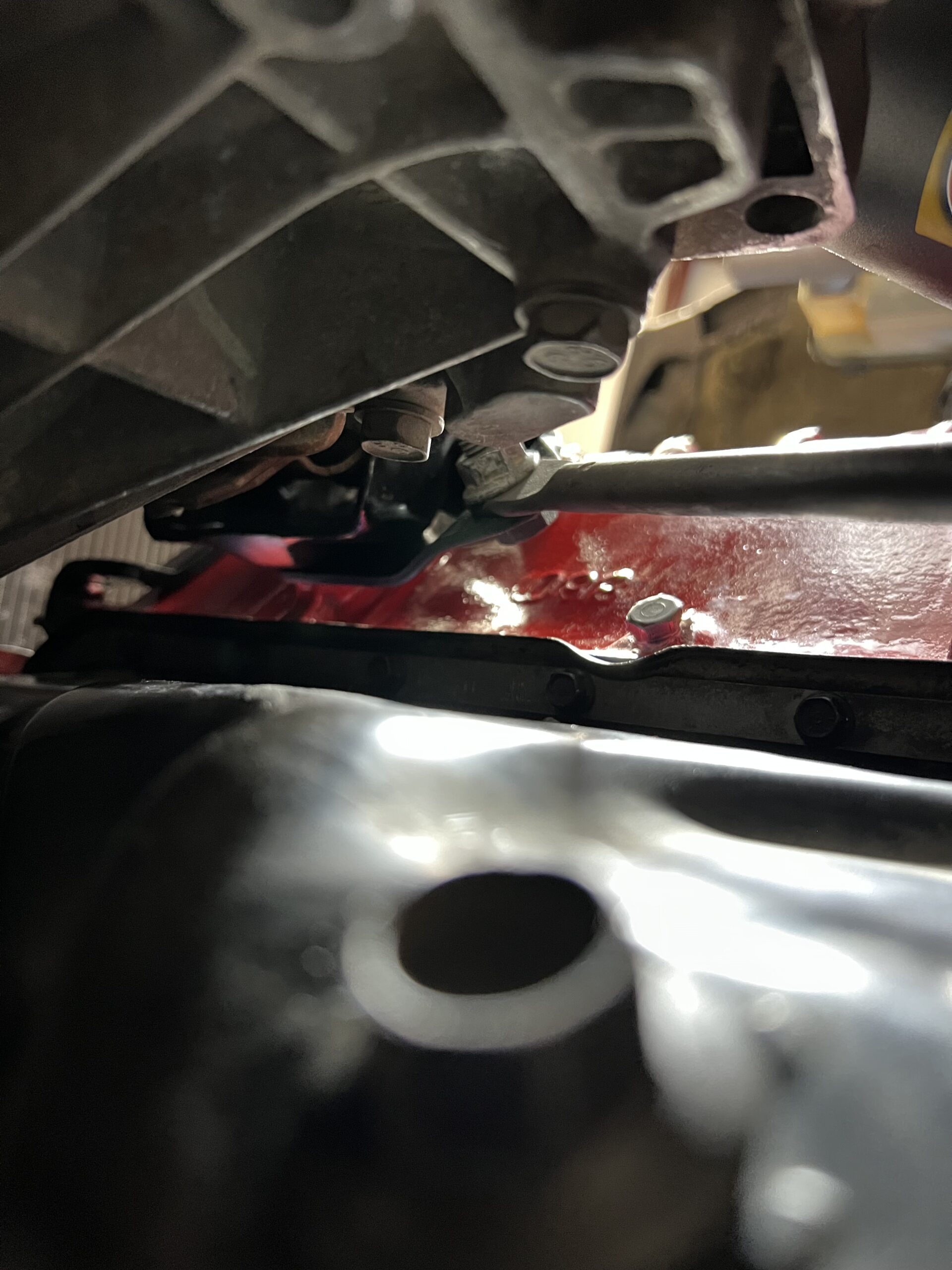
I ended up tightening that one from above. Doing so I impaled myself on part of the computer and the braking system. I really need to get some over fender creeper to be able to reach the back of the engine for the distributor and the grounding straps. That said, I decided to call it and possibly try to do some more later in the day.