Life as a large man can put a strain on many things. At 308lbs. that is especially true for anything that I sit on. Over the past few years. I have strained, damaged, and outright broken multiple seating apparatus. I even found that there is a limit to how far a seat belt will go. Now that I am headed back down the scale of obese, I understand I am never going to be a fragile flower and anything I plan on spending any time seated in needs to be of substantial construction.
When it comes to the shop I have a few items down there I use. I have a plastic rolling square “creeper” which looks very much like a short step but with casters on it. (think “very dangerous”)
I also have a very low rolling seat on curved metal side with a tray underneath also on casters.
The one I mainly use is a taller, five caster, round padded stool with a hydraulic post. It is pretty comfortable, but unfortunately it is too heavy, and the casters are crap. My significant bulk has bent them or cause som of the bearings to escape. I need to fix it. After looking for a way to fix the casters I realize I need to just replace them with larger stronger ones.
Maybe it was just a coincidence, but while watching motor trend TV. I saw an ad for a seriously Bas Ass creeper seat.
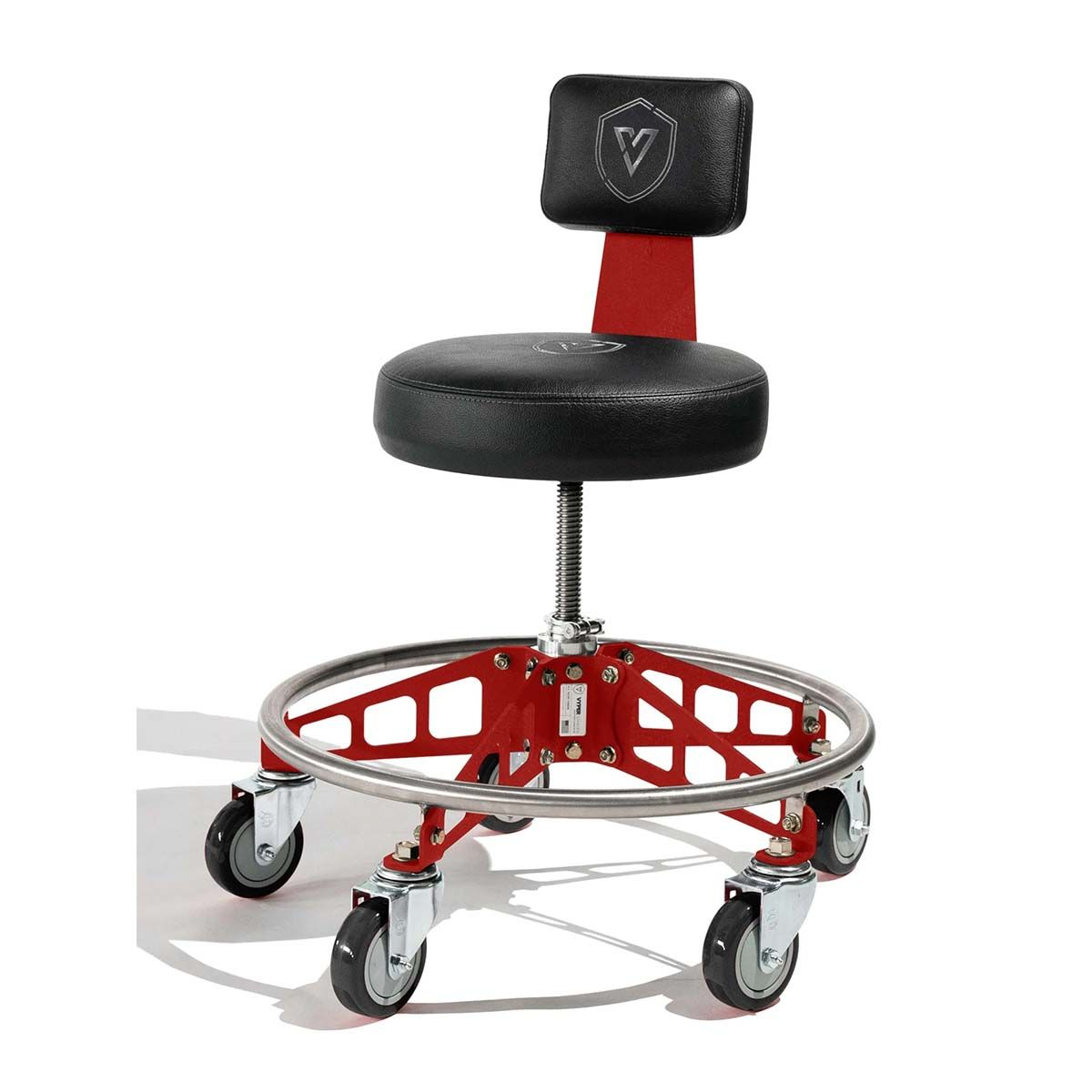
This thing is a BEAST. It is very well thought out. It is well designed, uses quality components and looks freakin’ awesome. It is made of aluminum and steel in an intelligent mix of lightness and strength. They upgraded to 4″ casters so it can roll over small junk on the floor easier. The bolts through the casters are hardened and can handle even my bulk. The height adjustment is done via an acme screw and a quick release clamp This combination will actually not slowly slip down to the bottom like my drum throne. As a matter of fact one of these with caster locks might make an excellent drum throne. But I digress. I would venture to say that this is the perfect Mechanics creeper.
Too bad I will never own one. I visited their amazing site (also nicely done) and to my surprise (not really) the price is astronomical. If I really think about it, for a professional mechanic, these are probably pretty reasonable prices. I paid over $1000 for my Aeron Desk chair with the rationale that I sit in it about 50 hours a week. Did I mention I have back issues? Unfortunately for a guy who only gets to spend about 8 hours in his shop per week. $500 for a rolling mechanics chair is too much. Besides I really want to see if I can build one of these. It would also be a “Valid” reason for me to buy a sewing machine capable of sewing leather.
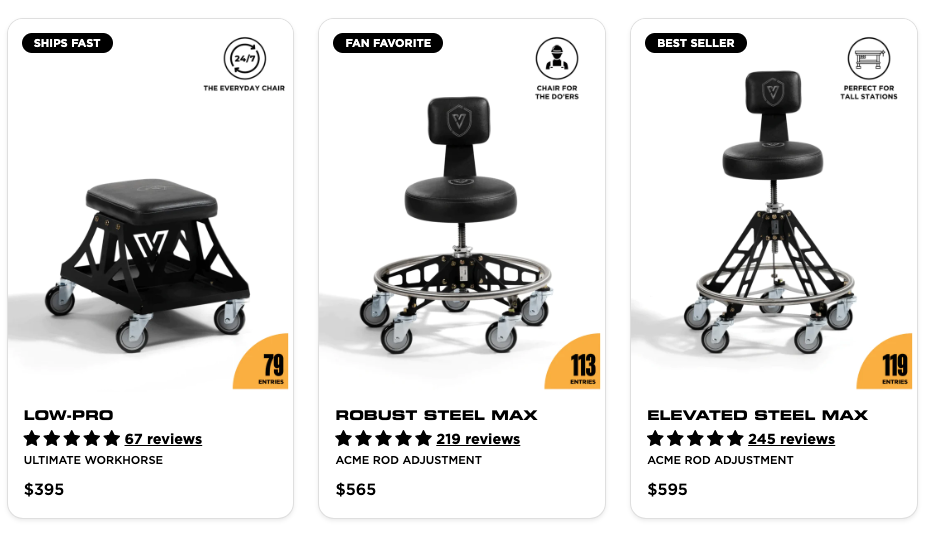
The plan for the home-made build:
Wheels: I have built multiple mobile bases for various appliances so I have experience using casters. I have 3″ casters on an angle iron base for my deep freeze in the garage. Which reminds me I still want to buy a Cricut to make stickers for the freezer. (another Project). I have sourced the 4″ no post casters for $15 each with brakes.
Legs: As far as the legs go, I was thinking of using plate aluminum with holes and bevels embossed into them. I don’t currently have the dimple dyes yet but this might be a good excuse to spend $200. As far as cutting the legs, I have a plasma cutter and I could make a wooden template to make them uniform. It would be better if I had a CNC machine to put the plasma cutter on, but that is definitely another project that I have not yet got to. I have a 6″ metal brake for my vice that should be able to handle the bends in the legs.
Foot rest: The foot rail I have already made with my ring roller. Actually 21 made and while I showed her how to use the ring roller. I just need to weld the ends together and add a couple of brackets to bolt through. Since it is aluminum, I really need to buy a better welder or at least get a spool gun to feed the aluminum wire (small but expensive project).
Seat: The actual seat is the upholstery part I need the sewing machine for, but I would be using leather not vinyl. The sewing machine is a cheap $100 job from China made for fixing shoes. It is a manual hand crank machine but with a little work a motor can be added that will make it much more usable. Now this is a full project to do that. As far as the rest of the seat, the base is just plywood with some captured nuts and predrilled holes, much better that wood screws. The foam is easy and I already have the old electric turkey carving knife down in the shop for cutting and shaping it.
Height adjustment: One of the build difficulties I was trying to wrap my head around was the acme screw. While they are available on Amazon, trying to cut the thread into the center boss would be somewhat difficult. After reviewing their site again. They have the solution. It happens to be an “upgrade” from their base model.
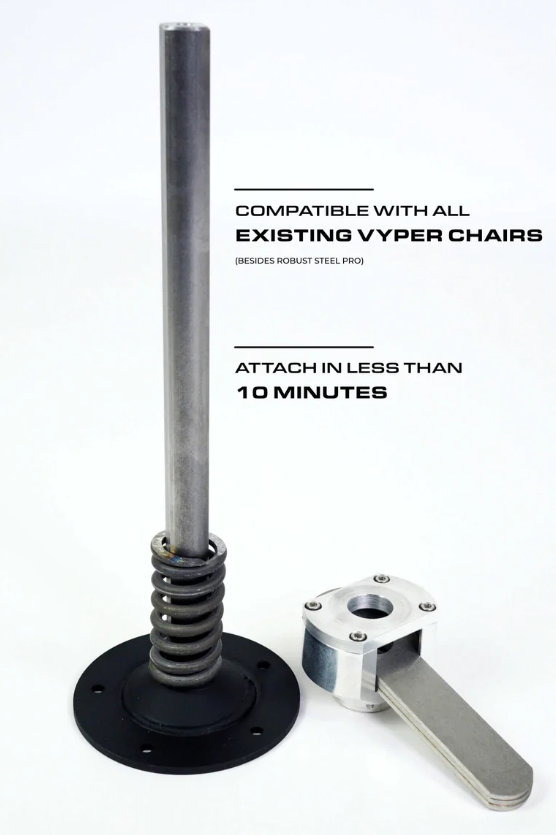
This little piece of engineering marvel shouldn’t be too hard to duplicate. The central shaft is easy, I have rod like this laying around the shop. The spring is a spare one off an engine valve, I have plenty of those. The base (top) is a flat piece of metal with a cone shaped support. As far as I can tell this is a solid piece of metal that is welded as a support to keep the top perpendicular to the shaft. This is the simplest solution but would require me to manufacture that part on the lathe. Since I haven’t fixed the lathe yet (another project), I think a smaller version of the base upside down would work. Five legs attached to a central pipe welded to both the top plate and the shaft. The lock mechanism is very simple just three flat bars with sharp edges set at a 20-30ยบ angle to the base that will jam against the shaft preventing it from lowering. The rest of the part is just to guide them into place and not allow them to lose that angle until lifted. I say it looks simple, but I need to actually try to make these pieces with my plethora of tools and junk pile of parts.
So you see I have already talked myself into the fact I can build one pretty easily. The fact that I don’t really have time and should be fixing my truck is inconsequential. I am saving money!